Fully Automatic Bag Packaging Production Line
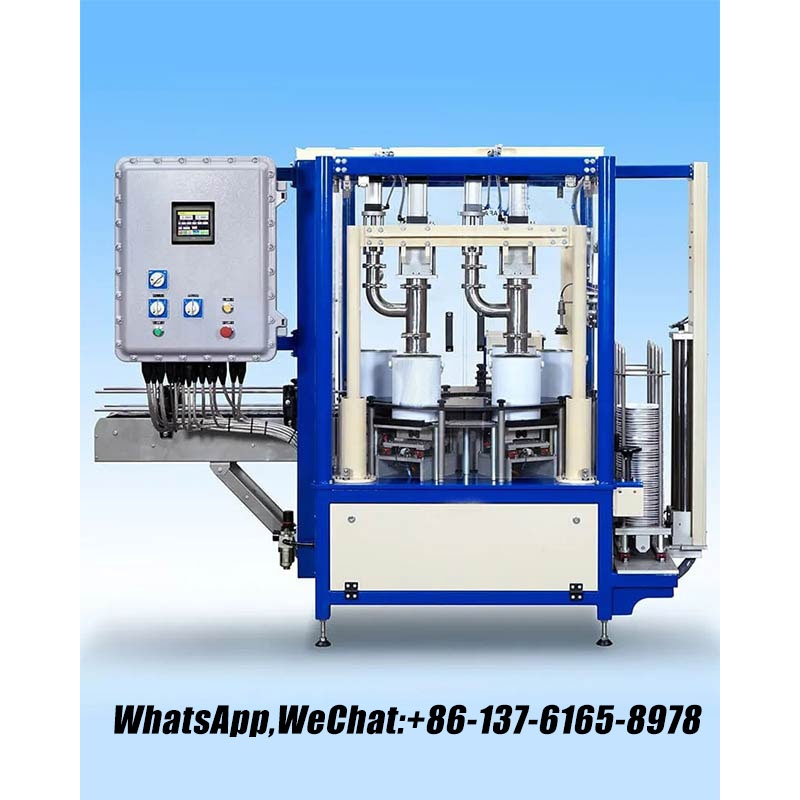
Fully Automatic Bag Packaging Production Line
A fully automatic bag packaging production line is a high-efficiency, integrated system designed for the automated filling, sealing, and packaging of products into bags. These lines are widely used in industries such as food, pharmaceuticals, chemicals, and agriculture to streamline operations, reduce labor costs, and ensure consistent quality. Below is a detailed overview of its components, features, benefits, and applications.
Key Components of the Production Line:
Bag Feeding System:
Automatic Bag Loader: Feeds empty bags into the production line from a storage hopper or carton.
Bag Opener: Mechanically opens bags to prepare them for filling.
Filling Machine:
Weighing System: Accurately measures the product by weight (e.g., using load cells).
Volumetric Filler: Dispenses product by volume for liquids or granular materials.
Net Weighing System: Ensures precise filling by weighing the filled bag before sealing.
Sealing Machine:
Heat Sealer: Seals the top of the bag using heat, suitable for plastic or laminated materials.
Ultrasonic Sealer: Uses ultrasonic waves for sealing, ideal for sensitive materials like powders or delicate foods.
Clipping or Stapling Device: For securing the top of the bag after sealing.
Conveyor System:
Infeed Conveyor: Transports empty bags to the filling machine.
Outfeed Conveyor: Moves filled and sealed bags to downstream processes (e.g., labeling, coding).
Labeling and Coding System:
Automatic Labeler: Applies labels to bags for branding, expiration dates, or barcodes.
Inkjet or Laser Coder: Prints production dates, batch numbers, or other information directly on the bag.
Quality Control System:
Metal Detector: Ensures no metal contaminants are present in the product.
Checkweigher: Verifies that each bag meets the target weight.
Vision System: Inspects seals and labels for defects.
Stacking or Palletizing System:
Automatic Stacker: Neatly stacks finished bags for manual or robotic palletizing.
Robotic Palletizer: Automates the stacking of bags onto pallets for efficient storage and transportation.
Control System:
PLC (Programmable Logic Controller): Centralizes control of the entire production line.
HMI (Human-Machine Interface): Touchscreen interface for easy operation, monitoring, and troubleshooting.
SCADA System: Provides real-time data logging and remote monitoring capabilities.
Key Features:
High Throughput:
Capacities range from 30 to 120 bags per minute, depending on the product and bag size.
Suitable for both small-scale and large-scale production.
Versatility:
Handles various products: powders, grains, liquids, granules, and solids.
Compatible with different bag types: pillow bags, stand-up pouches, flat bags, and more.
Precision and Accuracy:
Advanced weighing and filling systems ensure consistent product weights (±0.5% accuracy).
Seamless integration of checkweighers and metal detectors guarantees quality control.
User-Friendly Operation:
PLC and HMI systems allow for easy programming, parameter adjustment, and monitoring.
Recipe management enables quick changeovers between different products or bag sizes.
Safety and Compliance:
Meets global safety standards (e.g., CE, FDA, GMP) for food, pharmaceuticals, and chemicals.
Dust-tight and washdown-resistant designs for hygienic environments.
Modularity and Customization:
Scalable design allows for future expansion or upgrades (e.g., adding labeling or coding systems).
Customizable to fit specific product requirements, bag types, or production workflows.
Low Maintenance:
Robust construction with stainless steel or carbon steel components for durability.
Easy access to critical areas for cleaning and maintenance.
Benefits:
Increased Efficiency:
Fully automated process reduces labor costs and minimizes human error.
Consistent Quality:
Precise filling and sealing ensure uniform product weights and secure packaging.
High Productivity:
High-speed operation and minimal downtime maximize output.
Flexibility:
Adaptable to different products, bag types, and production requirements.
Cost Savings:
Reduces material waste, lowers labor costs, and minimizes product giveaway.
Compliance:
Ensures adherence to safety, hygiene, and regulatory standards.
Applications:
Food Industry:
Packaging of rice, flour, sugar, coffee, snacks, spices, and pet food.
Pharmaceuticals:
Filling and sealing of powders, tablets, capsules, and granular medications.
Chemicals and Petrochemicals:
Packaging of detergents, fertilizers, resins, and industrial powders.
Agriculture:
Bagging seeds, fertilizers, and animal feed.
Cosmetics and Personal Care:
Filling powders, creams, and gels into stand-up pouches or sachets.
Construction Materials:
Packaging cement, sand, plaster, and other powdered materials.
Why Choose a Fully Automatic Bag Packaging Line?
Labor Savings:
Eliminates the need for manual filling, sealing, and labeling.
Consistency:
Ensures uniform product weights and secure seals every time.
Scalability:
Modular design allows for future upgrades or expansion.
Hygiene:
Ideal for cleanroom or washdown environments in food and pharmaceuticals.
ROI:
High throughput and low maintenance costs deliver a rapid return on investment.
Invest in a fully automatic bag packaging production line to optimize your packaging operations, improve productivity, and ensure consistent product quality. With its scalability, versatility, and compliance with industry standards, this solution is ideal for businesses looking to streamline their packaging processes.